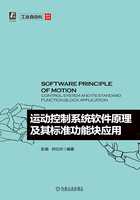
2.2.6 传动和控制技术
按动力源分类,传动系统除了机械传动系统外,还有液压传动、气动传动、电动传动、混合传动和新型传动系统等。表2-12是三种基本传动系统的比较。这里仅简单介绍液压和气动传动及有关的控制技术。
表2-12 基本传动系统的比较

1.液压传动和控制
液压传动利用液体的不可压缩性,将液压传递给执行机构实现控制的目的。它以液压油为工作介质,利用其静压力进行能量传递,具有结构简单、成本低且容易实现无级调速等特点,被广泛应用于各类大型传动系统。液压传动装置通常包括能源转换和存储装置、控制调节装置、执行装置和辅助装置等4部分。
液压系统中,用于控制和调节工作液体的压力高低、流量大小及改变流动方向的元件统称为液压控制元件或液压控制阀。液压控制阀通过对工作液体的压力、流量和液流方向的控制和调节,实现控制液压执行元件的开停和换向,调节其运动速度和输出转矩(或力),并对液压系统或液压元件进行安全保护等。
控制调节装置采用液压控制元件实现相应的控制功能。控制调节装置按其功能分为压力控制阀、流量控制阀和方向控制阀等。按控制方式分为开关阀、普通液压控制阀和电液压控制阀等。按安装方式分为管式、板式和插装式等类型。
能源转换装置用于提供液压油压力和流量。例如,液压泵、变排量液压泵和液压马达等。能量存储装置有各种蓄能器等。执行装置包括各种液压缸,例如,双作用单杆缸、单作用单杆缸、单作用伸缩缸及双作用磁性无杆缸等。
液压传动基本回路有压力控制回路、速度控制回路、方向控制回路以及其他液压控制回路等。
(1)压力控制回路
压力控制回路控制用于回路压力,使其适应负载要求,既能满足控制要求,又能降低动力消耗。
● 调压回路。用于控制整个液压系统或系统局部的油压,使之保持恒定或限制其最高值。
● 减压回路。用于使系统部分油路压力稳定地低于油源供压压力。
● 增压回路。用于使系统液压增高,满足高压回路的压力要求。
● 保压回路。用于保证液压恒定的控制回路。
● 卸荷回路。当执行元件不工作时,需要自动将泵源排出的液压油直通油箱,组成卸荷回路,使液压泵处于无载荷运转状态,达到减少动力消耗和降低系统发热的目的。
● 平衡回路。用于防止垂直或倾斜放置的液压缸和与之相连工作部件因自重而自行下落。
● 制动回路。液压马达带动部件运动的系统中,部件惯性只靠液压泵卸荷和停止供油是不够的。为此应设计制动控制回路。制动控制通常采用溢流阀等液压元件在液压马达回油路上产生背压,使液压马达受阻而被制动;也可用液压制动器产生摩擦力矩实现制动。
(2)速度控制回路
为解决不同执行元件不同的速度要求,要设置速度控制回路。
● 调速回路。调速控制回路在液压系统中占重要地位。用于调节液压执行机构的速度。常见速度控制回路有节流调速、容积调速和容积节流调速等。
● 增速回路。用于在不增加液压泵流量的条件下,使执行元件运行速度增加的控制回路。
● 减速回路。用于使执行元件由泵供给全流量的速度平稳降低,达到实际运行的速度要求。
● 同步回路。两个或两个以上液压执行元件需以相同位移或相同速度(或相同速比)同步运行时,采用同步回路。
(3)方向控制回路
为使执行元件起动、停止和改变运动方向,需要设置方向控制回路。方向控制回路用于控制进入执行元件的液流通断或流向。方向控制分阀控、泵控和执行元件控制三类。
(4)其他液压控制回路
除了压力控制回路、速度控制回路和方向控制回路外,液压系统中还有顺序动作回路、缓冲回路等。
● 顺序动作回路。用于实现多个执行元件的依次顺序动作,分为行程控制顺序动作、压力控制顺序动作和时间控制顺序动作等类型。
● 缓冲回路。为减少或消除执行元件在高速或大惯性运行状态突然停止或换向造成很大冲击和振动,需设置缓冲回路。
● 锁紧回路。用于执行元件停止工作时,将其锁紧在要求的位置。
● 油源回路。用于为液压系统提供有一定压力和流量传动介质的动力源回路。对其要求是能够提供压力稳定、流量均匀、系统可靠、传动介质温度稳定、节能和污染小的动力源。
(5)示例
组合机床的动力滑台是实现进给运动的一种通用部件。其运动靠液压缸驱动,滑台上安放各种专用切削头,根据需要还可安放动力箱、多轴箱、滑台和床身等通用部件。它可组合完成各种工件的钻、扩、铰、镗、铣、车、刮、攻螺纹等加工。
图2-22是某组合机床动力滑台液压传动系统的原理图。系统采用限压式变量叶片泵供油,液压缸差动连接以实现快速运动。

图2-22 某组合机床动力滑台液压传动系统原理图
1)电液换向阀换向:行程阀、液控顺序阀实现快进与工进的顺序切换;二位二通电磁阀实现一工进和二工进之间的速度换接;为保证进给尺寸准确度,用死挡铁停留限位。
2)组合机床典型工作循环:快进→一工进→二工进→死挡铁停留→快退→停止。
3)快进(差动连接):按起动按钮,三位五通电液动换向阀5的先导电磁换向阀1YA得电,阀芯右移,工作在左位,油路连接如下:
● 进油路。滤油器1→变量泵2→单向阀3→管路4→电液换向阀5的P口到A口→管路10、11→行程阀17→管路18→液压缸19左腔。
● 回油路。液压缸19右腔→管路20→电液换向阀5的B口到T口→管路8→单向阀9→管路11→行程阀17→管路18→缸19左腔。
● 形成差动连接回路。因快进时,滑台载荷较小,同时进油可经阀17直通油缸左腔,系统压力较低,因此,变量泵2输出流量大,使滑台快速前进。
4)第一次工进:快进行程结束,滑台上挡铁压下行程阀17,行程阀在上位工作,油路11和18断开。电磁铁1YA继续通电,电液动换向阀5仍在左位,电磁换向阀14的电磁铁3YA失励。进油路必须经调速阀12进入液压缸19左腔。同时,系统压力升高,将液控顺序阀7打开,并关闭单向阀9,因此,实现液压缸差动连接油路的切换。油路连接如下:
● 进油路:滤油器1→变量泵2→单向阀3→管路4→电液换向阀5的P口到A口→管路10→调速阀12→二位二通电磁换向阀14→油路18→液压缸19左腔。
● 回油路:液压缸19右腔→管路20→电液换向阀5的B口到T口→管路8→顺序阀7→背压阀6→油箱。
由于工作进给时,油压升高,变量泵2的流量自动减小,动力滑台进行第一次工作进给,进给量由调速阀12调节。
5)第二次工进:第一次工进结束,滑台上挡铁压下行程开关,使电磁换向阀14的电磁铁3YA励磁,阀14右位接入工作,切断该阀所在油路,经调速阀12的油液须经调速阀13才能进入液压缸19右腔,其他油路不变。由于调速阀13开口量小于阀12,因此,进给速度降低,第二次进给的速度由调速阀13调节。
6)死挡铁停留:动力滑台第二次工进结束时,碰上死挡铁,液压缸停止运动。系统压力进一步升高,达到压力继电器15的调定值,经延时后发送电信号,使动力滑台退回。退回前,滑台停留在死挡铁的限定位置。
7)快退:时间继电器延时时间到,发出电信号,使电液动换向阀5的电磁铁2YA励磁,1YA失电,同时,电磁换向阀14的3YA也失电。油路连接如下:
● 进油路。滤油器1→变量泵2→单向阀3→管路4→电液换向阀5的P口到B口→油路20→液压缸19右腔。
● 回油路。液压缸19右腔→管路18→单向阀16→油路11→电液动换向阀5的A口到T口→油箱。
8)原位停止:动力滑台退回到原始位置,挡铁压下行程开关,电磁铁1YA、2YA、3YA都失电,电液动换向阀5处于中位,动力滑台停止运动。变量泵输出油压升高,使泵流量自动减到最小。
表2-13是组合机床动力滑台液压传动系统中电磁铁和行程阀的关系。
表2-13 组合机床动力滑台液压传动系统中电磁铁和行程阀的关系

基本控制回路分析:该组合机床动力滑台采用如下基本控制回路。
● 容积节流调速回路。采用限压式变量泵和调速阀组成容积节流调速回路。它能满足系统调速范围大、低速稳定性好的要求,也能提高系统效率。系统在回油路增加一个背压阀6起到缓冲作用,改善速度稳定性,提高传动刚度,同时可使滑台承受与运动方向一致的一定的切削力。
● 快速回路。采用限压式变量泵和差动连接实现快进,不仅可获得较高运行速度,而且不致使系统效率过低。通常,动力滑台的快进和快退的速度可达最大速度的10倍。变量泵的流量自动变化,使在工进时只输出与液压缸所需相适应的流量,在快速行程输出最大流量,在死挡铁停留时只输出补偿系统泄漏所需的流量,因此,系统无溢流损失,效率高。
● 换向回路。采用电液动换向阀5实现换向,工作稳定可靠,用压力继电器和时间继电器发出的电信号作为换向切换的控制信号。
● 快速运动和工作进给的换接回路。采用行程换向阀实现速度换接,利用换向后系统的压力升高使远控顺序阀接通,使系统快速运动的差动连接转换到使回油排回油箱的连接。
● 两种工作进给的换接回路。采用两个调速阀串联回路实现两个工作进给的换接。
2.气动传动和控制
在我国,气动传动是在机械传动、电动传动和液压传动以后,才发展应用的传动方式。它以压缩空气为工作介质进行能量和信号灯传递,实现生产过程的自动化。气动传动和液压传动都属于流体传动。因此,它们性能类似。气动传动系统由气源装置、执行元件、控制元件和辅助元件组成。
①气源装置。获得压缩空气的设备,空气净化设备。如空压机,空气干燥机等。
②执行元件。将气体的压力能转换成机械能的装置,也是系统能量输出的装置。如气缸,气马达等。
③控制元件。控制压缩空气的压力、流量、流动方向以及系统执行元件工作程序的元件。如压力阀、流量阀、方向阀和逻辑元件等。
④辅助元件。起辅助作用,如过滤器、油雾器、消声器、散热器、冷却器、放大器及管件等。
气动驱动系统常用于两位式或有限点位控制的机器人,例如,冲压机器人、装配机器人的气动夹具等。