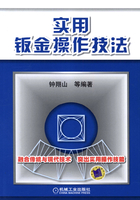
1.5 金属材料的加工性能
钣金零件加工工艺方案的确定除与加工零件的形状、精度及企业所具有的结构设备等有关外,还与零件所用的材料关系极大,即使是同一强度等级的材料,由于材料的化学成分不同,对零件的加工工艺也会带来不同的影响,从而直接影响着钣金件的生产加工。因此有必要分析并了解不同材料的加工工艺特性。
1.5.1 金属材料的加工工艺性
对于不同的金属,其加工工艺性能是不同的针对钣金加工的材料来讲,其加工工艺性能主要借助于工艺性能试验及工艺性能指标来衡量。
1.工艺性能试验
工艺性能试验是直接模拟某一类实际成形方式来成形小尺寸的试样,由于应力应变状态基本相同,故试验结果能更确切地反映实际工序中材料的受力情况和变形情况,因此对于特定工艺下的试验结果比较准确。
(1)弯曲和拉深试验 弯曲和拉深试验是实际生产中常用于评价板材局部弯曲伸长性能的试验。图1-8a所示的弯曲试验是将夹在特制钳口的板条作往复弯曲,依次向右侧及左侧弯曲90°,直至断裂或达到技术条件中规定的弯曲次数。折弯的半径r越小,反复弯曲的次数越多,其成形性能越好。这种试验主要用于鉴定厚度在2mm以下的板料。图1-8b所示为评价较厚板料弯曲性能的试验装置,当凸模弯曲直径d越小时,所弯角度越大,板料的弯曲成形性能越好。该试验可用于鉴定厚度在4mm以下的板料。图1-8c所示为Swift杯形件拉深试验,是以求极限拉深比LDR(Dmax/dp)作为评定板材拉深性能的试验方法,其凸模直径dP为32.50mm、圆角半径为4.5~5.5mm,适用板厚范围相应为0.32~1.3mm或者0.45~1.86mm。

图1-8 弯曲和拉深试验
a)、b)弯曲试验 c)拉深试验
1—凸模 2—压边圈 3—凹模 4—毛坯
用不同直径的平板毛坯拉深时,通常以拉深比0.025为单位改变毛坯直径,并以不发生破裂所能拉深成杯形件的最大毛坯直径Dmax与凸模直径dp之比作为极限拉深比LDR,同时,还要探索合适的压边力范围,以便减小其对LDR值的影响。
(2)胀形试验 艾利克森杯突试验和液压胀形试验均是评价各种板材胀形性能的试验。图1-9所示为艾利克森杯突试验装置(见图1-9a)以及试验标准极限杯突值(见图1-9b),这是一种国际上广泛采用的试验方法。

图1-9 胀形试验
a)杯突试验 b)标准杯突值
ISOR149规定,球形凸模半径ϕ20mm,凹模内径ϕ27mm、外径ϕ55mm,凸、凹模圆角半径均为0.75mm,压边圈厚度大于20mm、外径ϕ55mm,试验适用于0.5~2.0mm的板厚,且试样凹坑至边缘最短45mm以上。
GB/T4156—2007规定,球形凸模半径R10mm,压边圈尺寸未作规定,试件规格为70mm×80mm,其他参数与国际标准相同。试验适用于一般板厚≤2mm,必要时2~4mm的板料,且试验速度5~20mm/min。
2.工艺性能指标
材料对各种冲压成形方法的适应能力称为材料的冲压成形性能。材料的冲压成形性能好,就是指其便于冲压加工,单个冲压工序的极限变形程度和总的极限变形程度大,生产率高,成本低,容易得到高质量的冲压件。板料冲压成形性能是一个综合性的概念,冲压工艺性能应包括抗破裂性、贴模性和定形性等。
抗破裂性涉及板料在各种冲压成形工艺中的最大变形程度即成形极限,板料的冲压成形性能越好,板料的抗破裂性也越好,其成形极限就越高。
贴模性是指板料在冷压过程中取得与模具形状一致性的能力。成形过程中,由于各方面因素的影响,板料会产生内皱、翘曲、塌陷和鼓起等几何面缺陷,使贴模性降低。
定形性是指零件脱模后保持其在模内既得形状的能力。影响定形性的诸因素中,回弹是最主要的因素,零件脱模后,常因回弹过大而产生较大的形状误差,板料的贴模性和定形性是决定零件形状尺寸精度的重要因素。
以下几项力学性能指标能从不同角度反映材料的冲压性能,其中重要的几项有:
(1)均匀伸长率δb均匀伸长率δb是在拉伸实验中开始出现拉伸缩颈时的伸长率。它表示材料产生均匀变形或稳定变形的能力。一般情况下,冲压成形都是在板料的均匀变形范围内进行的,所以δb对冲压成形有较为直接的意义。δb越大,则材料的极限变形程度越大,越有利于冲压成形。
(2)屈强比(σs/σb)屈强比是一项反映材料冲压性能的综合性指标。屈强比小,屈服强度σs与强度极限σb之间的差值大,允许的塑性变形区间大,这对所有的冲压变形都是有利的。
(3)硬化指数n硬化指数n表示在冷塑性变形中材料的硬化程度。n值越大的材料,硬化效果越大,这对伸长类变形是有利的。由于变形硬化引起的变形抗力的增加可以补偿因拉伸导致的局部截面积减小所引起的承载能力的减弱,因此阻止了局部集中变形的进一步发展,具有扩展变形区,使变形区均匀,从而起到增加变形程度的作用。
(4)板厚方向性系数γ板厚方向性系数γ是指板料试样在拉伸实验时,宽度应变εb与厚度应变ε1的比值,故又称塑性应变比。冲压成形时,一般希望变形发生在板平面方向,而厚度方向则不希望发生过大的变化。当γ值大于1时,表示宽度方向的变形比厚度方向的变形更大,即γ值越大,越有利于提高板料冲压成形极限。
冲压加工所用板料都是经过轧制的材料,由于纤维组织的影响,其各个方向的力学性能并不一致,因此,板厚方向性系数是从各个不同方向取样,取其平均值作为标准的。
(5)板平面方向性Δγ当在板料平面内不同方向上截取实验试样时,实验中所测得的各种力学性能、物理性能等也不一样。板料这种力学性能、物理性能在板平面方向出现的各向异性,称为板平面方向性,用Δγ表示。板平面方向性的大小可以用板厚方向性系数在几个不同方向上的平均差别来衡量。板料的板平面方向性Δγ的存在,常会使拉深件口部出现凸耳,凸耳的大小和位置与Δγ有关,所以Δγ叫做凸耳参数。凸耳影响零件的形状和尺寸精度,必要时需增加切边工序。
1.5.2 常用钣金材料的工艺性能
了解并分析钣金材料的工艺性能对钣金件加工工艺以及生产操作规范的制订具有重要的意义,以下是一些常用钣金材料的加工工艺性能。
1.普通碳素结构钢的工艺性能
一般说来,钣金件以普通碳素结构钢(如Q195、Q215、Q235等)和优质碳素结构钢(如08、10F、20等)最为常用,该类钢种的冷或热成形、气割、碳弧气刨、水火矫形等工艺性都已趋于完善,除在成形上因材料厚度增加受变形率限制,加热受温度上限限制外,其他限制不多。
在加工较厚板料时,为增加板料的变形程度及降低板料的变形抗力,多用热成形或局部加热毛坯的拉深成形工艺,但应避免在某些温度区间加热,如碳钢加热到200~400℃时,因为时效作用(夹杂物以沉淀的形式在晶界滑移面上析出)使塑性降低,变形抗力增加,这个温度范围称为蓝脆区,这时钢的性能变坏,易于脆断,断口呈蓝色;而在800~950℃范围内,又会出现热脆区,使塑性降低。因此在板料热态拉深操作过程中,应特别注意实际变形热压的温度不应处于蓝脆区和热脆区。在操作时,应考虑加热设备与压力机间的位置对变形热压温度的影响,并谨慎使用降温吹风设备,以避免蓝脆及热脆的发生。
2.合金钢的工艺性能
常用于制造钣金结构件的合金钢通常为Q345(旧牌号为16Mn等)、Q390(旧牌号为15MnV等)等低合金高强度结构钢,它们的工艺性能分别为:
(1)Q345 Q345钢一般都是热轧状态供货,不需要热处理,特别是厚度小于20mm的轧材,其力学性能很高,因此热压后一般都直接使用。对于厚度大于20mm的钢板,为提高钢材的屈服强度和低温冲击韧度,可采用正火处理后使用。
另外,其气割性能与普通低碳结构钢相同。气割边缘1mm内虽有淬硬倾向,但由于淬硬区域很窄,可通过焊接消除,因此该钢种的气割边缘不需机械加工,可直接进行焊接。
碳弧气刨性能也与普通低碳结构钢相同。气刨边缘内虽有淬硬倾向,但由于淬硬区域也很窄,可通过焊接消除,因此该钢种的气刨边缘不需机械加工,可直接进行焊接。其结果与机械加工后进行焊接的热影响区硬度基本相同。
与Q235相比,Q345钢屈服强度都在345MPa以上,比Q235高,故冷成形力大于Q235钢。对于大厚度热轧钢材,采用正火或退火后,冷成形性能能得到极大的改善。但当板厚达到一定厚度(t≥32mm)时,须在冷成形后进行去应力热处理。
Q345钢当加热到800℃以上时,能获得良好的热成形性能,但加热温度不宜超过900℃,否则容易出现过热组织,降低钢材的冲击韧度。
此外,Q345钢经3次火焰加热矫形并水冷后的力学性能无明显改变,具有与原母材同样的抗脆性破坏能力,因此该钢种可以进行水火矫形,但对动载荷结构不宜采用水火矫形。
(2)Q390 较薄的Q390钢板的剪切与冷卷性能与Q345钢相似,但对板厚t≥25mm的热轧钢板,在剪切边缘上容易隐存因剪切的冷作硬化引起的小裂纹。这种裂纹有可能在钢材出厂前就已产生,因此,应加强质量检查,一经发现应经过气割或机械加工去除有裂纹的边缘。此外,较厚的Q390钢热轧板,冷卷时容易产生断裂,可通过930~1000℃的正火处理,提高其塑性和韧性,改善冷卷性能。
另外,该类钢的热成形和热矫形性能良好,加热温度为850~1100℃热成形时,多次加热对屈服强度的影响不大,且气割性能良好,碳弧气刨性能也良好,碳弧气刨对焊接接头的性能无不良影响。
3.不锈钢的工艺性能
不锈钢的种类很多,由于化学成分和金相组织的不同,各类不锈钢的力学性能、化学性质、物理性能也有较大差异,使不锈钢材料应用的工艺难度相对增加。
钣金加工中,常用的不锈钢牌号有两类:
甲类:马氏体型不锈钢,如12Cr13、20Cr13、30Cr13、40Cr13等。
乙类:奥氏体型不锈钢,如12Cr18Ni9Ti、12Cr18Ni9等。
上述两类不锈钢具有如下加工工艺性能:
1)为了获得好的塑性,应使材料处于软态,所以要进行热处理。甲类不锈钢的软化热处理是退火,乙类不锈钢的软化热处理是淬火。
2)在软态下,两类不锈钢的力学性能都具有较好的加工工艺性,特别是具有较好的冲压变形工艺性,适用于变形基本工序的冲压加工,但不锈钢的材料特性与普通碳钢相比是大不相同的,即使是拉深用不锈钢材料,其垂直塑性的异向性特性值也远低于普通碳钢,同时,又因为屈服强度高,冷作硬化严重,所以不仅在拉深过程中容易产生皱纹,而且板料在凹模圆角处产生的弯曲和反向弯曲变形引起的回弹,往往都会在制件的侧壁形成凹陷或挠曲,故对于不锈钢的拉深,需要有很高的压料力,而且要求对模具进行细致的调整。
由于不锈钢冷作硬化现象很强烈,拉深时容易产生皱褶,因此在实际操作过程中,要采取如下一些措施,以便保证拉深作业顺利进行:
①一般要在每次拉深后进行中间退火,这是因为不锈钢不像软钢那样可以经过3~5次拉深再进行中间退火,通常是每经过一次拉深后就要进行中间退火。
②变形量大的拉深件,最终拉深成形后,要紧接着进行消除残余内应力的热处理,否则拉深件会产生裂纹。去内应力的热处理规范是:甲类不锈钢加热温度250~400℃,乙类不锈钢加热温度350~450℃,然后在上述温度下保温1~3h。
③采用温热拉深方法可以得到较好的技术经济效果。例如对12Cr18Ni9不锈钢加热到80~120℃,能减少材料的加工硬化和残余内应力,提高拉深变形程度,减小拉深系数。但奥氏体不锈钢加热到较高温度(300~700℃)时,并不能进一步改善其冲压工艺性。
④拉深复杂零件时,应选用油压机、普通液压机等设备,使其在不高的拉深速度(0.15~0.25m/s)下变形,可以得到较好的效果。
3)与碳钢或非铁金属材料相比,不锈钢冲压另一特点是变形力大,弹性回跳大。因此,为保证冲压件尺寸和形状的精度要求,有时要增加修整、矫正以及必要的热处理。
4)奥氏体不锈钢不同品种间的屈服强度差别较大,因此,在剪切、成形的工序中需注意加工设备的承受能力。
4.非铁金属材料及其合金的工艺性能
由于非铁金属材料及其合金在成形过程中会接触到模具表面,因此对模具表面光滑程度的要求均较高。
(1)铜和铜合金 常用的铜和铜合金有纯铜、黄铜和青铜。纯铜和牌号为H62及H68的黄铜,冲压工艺性均好,比较起来,H62比H68的冷作硬化强烈。
青铜用作耐蚀、弹簧和耐磨零件,不同牌号间性能差别较大。一般说来,青铜比黄铜的冲压工艺性差些,且青铜比黄铜的冷作硬化强烈,需要频繁的中间退火。
大部分黄铜和青铜在热态下(600~800℃)具有较好的冲压工艺性,但加热会给生产上带来许多不便,并且铜和许多铜合金在200~400℃的状态下,塑性反而比室温时有较大的降低,因而一般不采用热态冲压。
(2)铝合金 钣金构件中常用的铝合金主要有铝锰或铝镁合金、铜铝合金、铝镁硅合金等。
铝锰或铝镁合金(相当于旧牌号的防锈铝)热处理效果很差,只能通过冷作硬化来提高强度,它具有适中的强度和优良的塑性及耐蚀性。铜铝合金(相当于旧牌号的硬铝)及铝镁硅合金(相当于旧牌号的锻铝)属于热处理能强化的铝合金。铝镁硅合金热状态下强度较高,热处理强化效果差,在退火状态下具有很好的塑性,适于冲压和锻造加工,铜铝合金强度较高,热处理强化效果好。
铝锰或铝镁合金可用退火方法来获得最大的塑性,铜铝合金及铝镁硅合金既可用退火方法也可用淬火方法来获得最大的塑性,它们在淬火以后的状态有较高的塑性和对冲压有利的综合力学性能,因而具有比退火状态更好的冲压工艺性。
铜铝合金及铝镁硅合金热处理强化有一个特点,即淬火后随时间延长逐渐强化,这种现象称为“时效强化”。时效强化具有一定的发展过程,不同牌号材料的发展速度也不相同。由于这类铝合金具有时效强化的特点,因此,对此类铝合金的冲压加工必须在时效强化发展完成之前进行,一般要求在淬火后1.5h内完成加工。
在铝合金中,铝镁合金的冷作硬化比较强烈,因此用这类材料制造复杂零件时,通常要进行1~3次中间退火,在深拉深成形后还要进行消除内应力的最终退火。
为改善加工工艺性,生产中还采用铝合金处于温热状态下冲压的工艺。温热冲压多用于冷作硬化后的材料,材料经温热(100~200℃)后,既保留了部分冷作硬化又改善了塑性,可以提高冲压变形程度和冲压件的尺寸精度。
温热冲压时,必须严格控制加热温度,过低会使冲压件产生裂纹,过高又会引起强度急剧降低,也会产生裂纹。在冲压过程中,凸模容易过热,当它超过一定温度后,就会使冲压材料强烈软化,引起拉深件断裂。凸模温度保持在小于60℃,可以提高温热拉深的变形程度。温热冲压中,必须采用特制的耐热润滑剂。
(3)钛和钛合金 钛和钛合金的工艺性较差,其强度较高,变形力大,冷作硬化程度强烈,除少数牌号可以对变形不大的零件进行冲压外,大多采用热冲压。热冲压的加热温度较高(300~750℃),且因牌号不同而不同,加热温度过高会使材料变脆,不利于冲压。由于钛是一种化学性质非常活跃的元素,与氧、氢、氮等元素的化合所需温度都不高,而与氧、氢、氮等生成的化合物都是产生脆性的主要因素,因此,钛及钛合金的加热受到严格的限制。需要高温加工时,必须在保护气体中进行,或采用全保护的无泄漏包装进行整体加热。在生产钛和钛合金的冲压件时,应采取尽可能低的冲压速度。
此外,钛材的切断可采用机械方法,如锯切、高压水切割、车床切割、管切断机床切割等。锯切速度宜慢,绝不可以用氧乙炔焰等通过加热的方法进行气割,也不宜用砂轮锯切割,以免切口的热影响区受到气体的污染。同时,切口处飞边过大,还要增加飞边处理的工序。
钛和钛合金管可以冷弯,但回弹现象明显,回弹量通常在室温下是不锈钢的2~3倍,因此,钛管的冷弯要处理好回弹量。此外,钛管的冷弯弯曲半径不得小于管外径的3.5倍。冷弯时,可在管内填充经过干燥的河沙,并用木锤或铜锤夯实,以防止局部出现圆度超差或皱褶现象。弯管机冷弯时,应加芯轴。热弯时,预热温度应在200~300℃之间。
若需90°翻边,应分别用30°、60°、90°三套模具分次压制,以免出现裂纹。