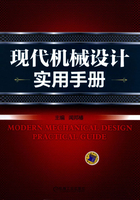
4 常用几何公式及截面的力学特性公式
4.1 常用几何体公式
(见表1.1-23)
表1.1-23 常用几何体的体积、面积及重心位置
(续)
4.2 截面几何及力学特性公式
(见表1.1-24、表1.1-25)
表1.1-24 截面几何及力学特性公式
(续)
(续)
(续)
注:A—面积;I—惯性矩;W—截面系数;W=I/e;e—形心S到相应位置的距离;i—惯性半径,。
表1.1-25 常用组合截面的回转半径
(续)
第2章 一般标准和设计规范
1 一般标准和金属切削加工零件的设计规范
1.1 标准尺寸
(见表1.2-1)
表1.2-1 标准尺寸(摘自GB/T 2822—2005) (mm)
注:1.“标准尺寸”为直径、长度、高度等系列尺寸。
2.R′系列中的黑体宇,为R系列相应各项优先数的化整值。
3.选择尺寸时,优先选用R系列,按照R10、R20、R40顺序。如必须将数值圆整,可选择相应的R′系列,应按照R′10、R′20、R′40顺序选择。
1.2 机器轴高
(见表1.2-2)
表1.2-2 机器轴高(摘自GB/T 12217—2005)(mm)
注:1.机器轴高h不包括安装所用的垫片在内,如果机器需配备绝缘垫片时,其垫片的厚度应包括在内。
2.机器轴高优先选用第Ⅰ系列数值,如果不能满足需要时,可选用第Ⅱ系列值,其次选用第Ⅲ系列的数值,第Ⅳ系列的数值尽量不采用。
3.当轴高大于1600mm时,推荐选用160~1000mm范围内的数值再乘以10。
4.对于支承平面不在底部的机器,应按轴伸轴线到机器底部的距离选取极限偏差及平行度公差。L为轴的全长。
1.3 机器轴伸
(见表1.2-3~表1.2-7)
表1.2-3 圆柱形轴伸(摘自GB/T 1569—2005) (mm)
表1.2-4 直径220mm以下的圆锥形轴伸形式与尺寸(摘自GB/T 1570—2005) (mm)
(续)
注:1.φ220mm及以下的圆锥轴伸键槽底面与圆锥轴线平行。
2.键槽深度t可由测量G来代替,或按表1.2-6的规定,测量t2。
3.L2可根据需要选取小于表中的数值。
表1.2-5 直径220mm以上的圆锥形轴伸形式与尺寸(摘自GB/T 157O—2OO5) (mm)
注:1.L2可根据需要选取小于表中的数值。
2.本标准规定了1:10圆锥形轴伸的形式和尺寸,适用于一般机器之间的连接并传递转矩的场合。
表1.2-6 圆锥形轴伸大端处键槽深度尺寸(摘自GB/T 1570—2005) (mm)
注:对键槽底面平行于轴线的键槽,当按照轴伸大端直径来检验键槽深度时,其数值应符合本表中t2的规定,t2的极限偏差与t的极限偏差相同,此时表1.2-4中的t1作为参考尺寸。
表1.2-7 圆锥形轴伸L1的轴向极限偏差(摘自GB/T 157O—2005) (mm)
注:1.基本直径d的公差选用GB/T 1800.1及GB/T 1800.2中的IT8。
2.1:10的圆锥角公差选用GB/T 11334中的AT6。
1.4 棱体的角度与斜度
(见表1.2-8、表1.2-9)
表1.2-8 棱体的角度和斜度(摘自GB/T 4096—2001)
(续)
表1.2-9 标准角度
注:1.本标准为一般用途的标准角度,不适用于由特定尺寸或参数所确定的角度以及工艺和使用上有特殊要求的角度。
2.选用时优先选用第一系列,其次是第二系列,再次是第三系列。
3.该表不属于GB/T 4096—2001的内容,仅供参考。
1.5 圆锥的锥度与锥角系列
(见表1.2-10~表1.2-12)
表1.2-10 一般用途圆锥的锥度与锥角(摘自GB/T 157—2001)
(续)
注:1.系列1中120°~1:3的数值近似按R10/2优先数系列,1:5~1:500按R10/3优先数系列(见GB/T 321)。
2.优先选用系列1,其次选用系列2。
表1.2-11 特定用途圆锥的锥度与锥角(摘自GB/T 157—2001)
表1.2-12 莫氏和公制锥度(附斜度对照)
注:1.公制圆锥号数表示圆锥的大端直径,如80号公制圆锥,它的大端直径即为8Omm。
2.莫氏锥度目前在钻头及铰刀的锥柄、车床零件等应用较多。
1.6 中心孔
(见表1.2-13、表1.2-14)
表1.2-13 60°中心孔(摘自GB/T 145—2001) (mm)
注:1.括号内尺寸尽量不用。
2.A、B型中尺寸l1取决于中心钻的长度,即使中心孔重磨后再使用,此值不应小于t值。
3.A型同时列出了D和l2尺寸,B型同时列出了D2和l2尺寸,制造厂可分别任选其中一个尺寸。
表1.2-14 75。、90。中心孔(JB/ZQ 4236—2006、JB/ZQ 4237—2006) (mm)
注:1.中心孔的选择:中心孔的尺寸主要根据毛坯轴端直径DO和零件毛坯总质量(如轴上装有齿轮、齿圈及其他零件等)来选择。若毛坯总质量超过表中DO相对应的质量时,则依据毛坯质量确定中心孔尺寸。
2.当加工零件毛坯总质量超过500Okg时,一般宜选择B型中心孔。
3.D型中心孔是属于中间形式,在制造时要考虑到在机床上加工去掉余量“L3”以后,应与B型中心孔相同。
4.中心孔的表面粗糙度按用途自行规定。
1.7 零件的倒圆、倒角
(见表1.2-15)
表1.2-15 零件倒圆与倒角(摘自GB/T 64O3.4—2008) (mm)
(续)
1.8 圆形零件自由表面过渡圆角半径和静配合连接轴用倒角
(见表1.2-16、表1.2-17)
表1.2-16 圆形零件自由表面过渡圆角半径和静配合连接轴用倒角 (mm)
注:尺寸D-d是表中数值的中间值时,则按较小尺寸来选取R。例如D-d=98,则按9O选R=25。
表1.2-17 过渡配合、静配合嵌入倒角 (mm)
1.9 球面半径
(见表1.2-18)
表1.2-18 球面半径(摘自GB/T 64O3.1—2008) (mm)
1.10 燕尾槽
(见表1.2-19)
表1.2-19 燕尾槽(JB/ZQ4241—2006) (mm)
注:1.“A”的系列为:40,45,50,55,60,65,70,80,90,100,110,125,140,160,18O,200,225,250,280,320,360,400,450,500。
2.“C”为推荐值。
1.11 T形槽
(见表1.2-20)
表1.2-20 T形槽(摘自GB/T 158—1996) (mm)
(续)
注:螺母材料为45钢。螺母表面粗糙度(按GB/T 1031)最大允许值,基准槽用螺母的E面和F面为Ra3.2μm;其余为Ra6.3μm。螺母进行热处理,硬度为35HRC,并发蓝。
1.12 弧形槽端部半径
(见表1.2-21)
表1.2-21 弧形槽端部半径 (mm)
注:d是铣削键槽时键槽弧形部分的直径。
1.13 砂轮越程槽
(见表1.2-22)
表1.2-22 砂轮越程槽(摘自GB/T 6403.5—2008) (mm)
(续)
1.14 刨切、插切、珩磨越程槽
(见表1.2-23)
表1.2-23 刨切、插切、珩磨越程槽 (mm)
1.15 退刀槽
(见表1.2-24)
表1.2-24 退刀槽(摘自JB/ZQ 4238—2006) (mm)
(续)
1.16 插齿、滚齿退刀槽
(见表1.2-25~表1.2-27)
表1.2-25 插齿空刀槽(摘自JB/ZQ 4238—2006) (mm)
表1.2-26 滚人字齿轮退刀槽(摘自JB/ZQ 4238—2006) (mm)
表1.2-27 滑移齿轮的齿端圆齿和倒角尺寸 (mm)
1.17 滚花
(见表1.2-28)
表1.2-28 滚花(摘自GB/T 64O3.3—2008) (mm)
注:1.表中h=O.785m-O.414r。
2.滚花前工件表面粗糙度的轮廓算术平均偏差Ra的最大允许值为12.5μm。
3.滚花后工件直径大于滚花前直径,其值Δ≈(0.8~1.6)m,m为模数。
1.18 分度盘和标尺刻度
(见表1.2-29)
表1.2-29 分度盘和标尺刻度(JB/ZQ 4260—2006) (mm)
注:1.数宇可按打印宇头型号选用。
2.尺寸h1在工作图上不必注出。
1.19 锯缝尺寸
(见表1.2-30)
表1.2-30 锯缝尺寸(摘自JB/ZQ 4246—2006) (mm)
(续)