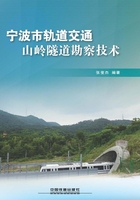
1.3 山岭隧道主要施工方法
山岭隧道施工方法依据工程地质、水文地质条件,结合隧道的断面尺寸、长度、衬砌类型、使用功能、施工技术水平等因素综合研究确定,主要考虑的因素是围岩稳定性。围岩是隧道的主要承载体,隧道施工的技术原则是在施工中充分保护围岩,避免过度破坏和损伤遗留围岩的强度,使暴露的围岩尽量保留既有的质量,为了充分发挥围岩的结构作用,应容许围岩有可控制的变形。山岭隧道施工方法主要分为矿山法(钻爆法)和掘进机法。山岭岩质隧道的开挖技术随着科学技术的发展大体经历了四个发展阶段——第一阶段:钢钎大锤;第二阶段:手持风钻;第三阶段:凿岩台车;第四阶段:隧道掘进机(TBM)法。第一阶段~第三阶段均属于矿山法(钻爆法);第四阶段为目前较为先进的隧道掘进机(TBM)法,其在隧道施工中的应用越来越广泛。岩质隧道开挖技术发展示意图如图1-3所示。
1.3.1 矿山法(钻爆法)
山岭隧道的常规施工方法称为矿山法,因最早应用于采矿坑道而得名,而多数情况下需要采用钻眼爆破进行开挖,因此也常称为钻爆法。矿山法根据围岩的级别主要采用的方法有全断面开挖法、上下台阶法、中隔墙法、交叉中隔墙法、双侧壁导坑法等,在同时考虑施工进度及工程投资时,施工方法优先选择顺序一般为:①全断面法;②上下台阶法;③中隔墙法(CD);④交叉中隔墙法(CRD);⑤双侧壁导坑法,上述5种施工方法的安全性和投资一般是依次逐步增大的,其施工的进度是逐步减慢的。各施工方法的适用性具体如下:
1.全断面开挖法
全断面开挖法是指将整个隧道开挖断面一次钻孔、一次爆破成型、一次初期支护到位的隧道开挖方法。全断面开挖法的优点是:洞内施工作业空间较大,工序少,利于大型配套机械化作业,施工效率较高,施工操作简单,利于施工组织和管理,同时全断面开挖减少了爆破振动次数,降低了对围岩的扰动。缺点是:由于开挖面较大,围岩相对稳定性降低,且每个循环工作量较大,每次深孔爆破引起的振动较大,因此要求具有较强的开挖、出渣能力和相应的支护能力。一般在围岩等级为Ⅰ~Ⅱ级硬岩地层时采用该方法,在开挖时可根据具体围岩情况,调整开挖进尺,增加施工安全度。浅埋段、偏压段和洞口段不宜采用全断面法开挖。全断面法开挖示意图如图1-4所示。

图1-3 岩质隧道开挖技术发展示意图
2.上下台阶法
上下台阶法是将断面分成上、下两个台阶开挖,上台阶长度一般控制在1~1.5倍洞径,上台阶开挖好后必须在地层失去自稳能力之前尽快开挖下台阶,使支护形成封闭结构。当开挖中发现围岩较差时,为了稳定工作面,可辅以超前小导管支护、预留核心土法等措施。预留核心土法是在上下台阶法的基础上,遇到围岩较差时,采用上台阶取1倍洞径左右环形开挖,留核心土,用小导管超前支护并预注浆以稳定工作面,必要时可用网构钢拱架作初期支护,拱脚、墙脚设置锁脚锚杆。上下台阶法开挖示意图如图1-5所示。
上下台阶法施工,其优点是灵活多变、适用性强,能保证足够的作业空间且施工速度较快,并能使支护体系较早的闭合,利于开挖面的稳定性和控制其结构变形以及由此引起的地面沉降。缺点是上、下部作业互相干扰,尤其是短台阶干扰较大,应注意下部作业对上部稳定性的影响,并注意台阶开挖会增加对围岩的扰动次数等。另外,上下台阶法施工时,围岩稳定性愈差,闭合时间要求愈短,对施工的组织设计影响较大,所以开挖过程中对围岩等级及风险预估能力的要求较高。

图1-4 全断面法开挖示意图
1—全断面开挖;Ⅱ—初期支护;3—隧道底部开挖;Ⅳ—底板(仰拱)浇筑;Ⅴ—拱墙二次衬砌

图1-5 上下台阶法开挖示意图
上下台阶法在Ⅱ、Ⅲ级围岩地层中使用较为广泛。
3.中隔墙法
中隔墙法也称CD工法(Center Diaphragm),是以台阶法为基础,沿着隧道的一侧,从上往下分两部分或三部分进行开挖,将隧道断面从中间分成左、右两部分,每一部分开挖并支护后形成独立的闭合单元。通过隧道断面中部的临时支撑隔墙,将断面跨度一分为二,减小了开挖断面跨度,使断面受力更合理,从而使隧道开挖更加安全、可靠。
采用该法进行隧道开挖时,台阶长度一般为1~1.5倍洞径(此处洞径取分部高度和跨度的大值)。先开挖一侧断面与后开挖断面的间距一般按1~1.5倍洞径进行控制。为了稳定工作面,可采取超前大管棚、超前锚杆、超前小管棚、超前预注浆等辅助施工措施进行超前加固。
中隔墙法主要适用于地层较差的Ⅳ、Ⅴ级围岩地层、不稳定岩体和浅埋段、偏压段、洞口段。一般采用人工开挖,人工和机械配合出渣。为了提高施工速度和减小施工难度,也可适当采用小剂量炸药来控制爆破范围,以免破坏已完成的临时支撑隔墙。
4.交叉中隔墙法
交叉中隔墙法也称CRD工法(Cross Diaphragm),当CD工法仍不能保证围岩稳定和隧道施工安全要求时,可在CD工法的基础上对各分部加设临时仰拱,将原CD工法先开挖中壁一侧改为两侧交叉开挖、步步封闭成环而改进发展的一种工法。CRD工法各分部间应拉开一定的距离,距离以保证掌子面稳定为准,一般为1~1.5倍洞径(此处洞径取分部高度和跨度的大值),为满足操作空间要求,在能够保证掌子面围岩稳定的情况下,可适当缩短距离。交叉中隔壁法开挖示意图如图1-6所示。
交叉中隔墙法的优点是:将大断面施工化成小断面施工,使得每个小断面都在短时间内封闭成环,能够控制早期围岩变形,利于施工安全。该方法的缺点是:由于将大断面分割成了多个小断面,只能采取小型机械或人工开挖及运输作业,且分块太多,工序繁多、复杂,进度较慢。临时支撑的施作和拆除困难,成本较高。当需要采用爆破时,必须严格控制药量,避免损坏中隔墙(育王岭隧道施工中曾出现该种情况)。CRD工法适用于较差地层,特别破碎的岩石、坡洪积层(碎石土、卵石土、圆砾土、角砾土)及黏性土组成的Ⅴ级围岩及较差围岩中的洞口段、浅埋段等。另据资料显示,在浅埋隧道沉降控制方面,CRD工法优于CD工法,前者比后者减少地面沉降近50%。

图1-6 交叉中隔壁法开挖示意图
Ⅰ—超前支护;1—左侧上部开挖;Ⅱ—左侧上部初期支护;2—左侧中部开挖;Ⅲ—左侧中部初期支护;3—左侧下部开挖;Ⅳ—左侧下部初期支护;4—右侧上部开挖;Ⅴ—右侧上部初期支护;5—右侧中部开挖;Ⅵ—右侧中部初期支护;6—右侧下部开挖;Ⅶ—右侧下部初期支护;7—拆除中隔墙;Ⅷ—仰拱及填充混凝土;Ⅸ—拱墙二次衬砌
5.双侧壁导坑法
双侧壁导坑法是双侧壁导坑超前中间台阶法的简称,也称眼镜(睛)工法,也是变大跨度为小跨度的施工方法。双侧壁导坑法以台阶法为基础,将隧道断面分成双侧壁导洞和上、下台阶4部分,将大跨度分成3个小跨度,其双侧壁导洞尺寸的确定以满足机械设备和施工条件为主。双侧壁导坑法开挖示意图如图1-7所示。
双侧壁导坑法主要适用于断面很大,地层较差的Ⅳ、Ⅴ级围岩地层,不稳定岩体和浅埋段、偏压段、洞口段。轨道交通工程因隧道断面较小,施工机械作业困难,对施工进度控制不利,所以一般不采用该方法。

图1-7 双侧壁导坑法开挖示意图
1—右侧上导坑开挖;2—右侧下导坑开挖;3—左侧上导坑开挖;4—左侧下导坑开挖;5—中间上导坑开挖;6—中间下导坑开挖
1.3.2 隧道掘进机(TBM)法
掘进机法包括隧道掘进机法和盾构掘进机法,本书仅针对隧道掘进机(TBM)法进行说明。隧道掘进机(Tunnel Boring Machine),简称TBM,是利用回转刀具切削破岩及掘进,形成整个隧道断面的一种新型、先进的隧道施工机械。
隧道掘进机(TBM)根据支护形式分为开敞式、单护盾式、双护盾式3种类型,分别如图1-8、图1-9、图1-10所示。

图1-8 开敞式隧道掘进机
1.开敞式TBM
利用岩壁的反作用力,实现掘进功能所需的反推力和反扭矩,在常温常压下,实现隧道掘进一次成型、初期支护、出渣运输功能,集机、电、液、气于一体,实现隧道施工自动化、工厂化的大型综合性施工设备。配置钢拱架安装器与喷锚等辅助设备,常用于硬岩,采取有效支护手段后也可应用于软岩隧道。

图1-9 单护盾式隧道掘进机

图1-10 双护盾式隧道掘进机
2.单护盾式TBM
单护盾式TBM推进时利用管片作支撑,其原理类似于盾构。与双护盾式TBM相比,掘进与安装管片不能同时进行。单护盾式TBM常用于软岩及地下水位较高的不稳定地层施工。
3.双护盾式TBM
双护盾掘进机是在整机外围设置与机器直径相一致的圆筒形护盾结构,以利于掘进松软破碎或复杂岩层的全断面岩石掘进机。双护盾掘进机在遇到软岩时,软岩不能承受支撑板的压应力,由盾尾推进液压缸支撑在已拼装的预制衬砌块上或钢圈梁上以推进刀盘破岩前进;遇到硬岩时,与敞开式掘进机的工作原理一样,靠支撑板撑紧洞壁,由主推进液压缸推进刀盘破岩前进。双护盾式TBM的一般结构组成:装有刀盘及刀盘驱动装置的前护盾,装有支撑装置的后护盾(支撑护盾),连接前、后护盾的伸缩部分和安装预制混凝土管片的尾盾。双护盾式TBM又称伸缩护盾式TBM,具有两种掘进模式(单/双护盾掘进模式),既可用于硬岩又可用于软岩,常用于混合地层施工,适应性非常广泛,能安全地穿过断层破碎地带。
双护盾式TBM开挖与衬砌同步,采用管片支护,支护速度快,隧道一次成型;硬岩掘进的适应性同敞开式TBM,软弱围岩能采用单护盾模式掘进,比敞开式有更好的适应性。与敞开式TBM相比,对地质变化的适应能力更强;设备与人员处于TBM壳体的保护下,安全性好。
4.隧道掘进机(TBM)法施工的优缺点
(1)优点
1)施工效率高:施工速度快,约为矿山法的4~6倍,机械化、自动化及信息化程度高,可节约人工劳动,施工效率较高。
2)施工质量好:洞壁光滑美观,超挖量少,施工后质量较好,节约衬砌。
3)对围岩扰动小:采用非爆破开挖,尘土、气体、噪声污染小,施工时较常规方法减少了对辅助洞室及地表的破坏,施工阶段对周边环境的污染减少了,利于环保。
4)施工安全性高:隧道掘进机可在防护棚内进行刀具更换,密闭式操纵室和高性能集成机的使用使安全性和作业环境有了极大的改善。
(2)缺点
1)掘进机对多变地质条件如断层破碎带、挤压带、涌水地段等的适应性较差。TMB法适用于中硬岩层,岩石单轴抗压强度介于20~250MPa之间,其中在岩石单轴抗压强度50~100MPa的岩层中施工时工效较高;地质条件对TBM掘进效率影响很大,在良好岩层中月进尺可达500~600m,而在破碎岩层中只有100m左右,在塌陷、涌水、暗河地段甚至需停机处理,所以选用TBM开挖隧道应尽量避开复杂不良岩层。
2)掘进机结构复杂,对材料、零部件的耐久性要求高,设备购置和维护成本高,一般不适宜短隧道开挖。TBM工作中附带的后续设备长100~200m,因此在正式采用TMB进行掘进前,需先采用钻爆法施工一段长200m左右的隧道。所以,一般一次性连续开挖长度不宜短于1km,开挖长度3~8km时采用TBM法较为有利。
3)施工过程中不能改变开挖断面和形状,在应用上受到限制。TBM一般只适用于圆形断面隧道,只有铣削滚筒式掘进机可在软岩中掘进非圆形断面隧道。开挖隧道直径在1.8~12m之间,以直径3~6m最为成熟。
4)TBM进场准备时间较长。根据其直径与型式、运输途径、组装基地状况等不同,需准备1~2个月时间。
在当前轨道交通山岭隧道施工实践及相类似断面的公路隧道中,采用最多的方法是台阶法,其次是全断面法。在大断面隧道中,双侧壁导坑法(眼镜法)采用较多。由于施工机械的发展和辅助工法的采用,更多地采用全断面法,特别是全断面法与超短台阶法相结合。