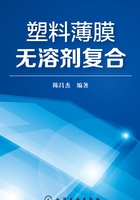
第一节 共挤出复合工艺
一、何谓共挤出复合
共挤出复合指通过两台及两台以上的挤出机,分别将两种及两种以上的不同性能的塑料颗粒(或粉体)熔融塑化,并通过一个共挤出模头,制取多层复合薄膜的工艺,也称为共挤出多层复合成膜工艺。
共挤出多层复合成膜工艺,是在单层挤出薄膜生产工艺的基础上发展而成的一种制造多层塑料薄膜的工艺。它是挤出成膜工艺的一个重要的分支,其本质上仍然是一种挤出复合工艺,因此具有挤出成膜工艺的基本特征,即直接由塑料粒子(或粉状物料)经挤出成型,一次生产出复合薄膜,具有工艺路线短和节约人力、物力及能耗低的优点。在正常生产条件下,采用该工艺生产时,塑料全部转变为塑料薄膜,没有任何有毒有害的物质产生,不对生产车间及周边环境产生污染,是典型的“绿色包装工艺”,于人类的可持续发展十分有利,因此它被人们认为是塑料软包装行业转型发展的首选工艺之一。同时共挤出多层复合成膜工艺通过各种不同的原料(或不同配方)的搭配,组成各自不同的多层结构,实现塑料薄膜的高功能化从而显著地提高薄膜的使用效果或者明显地降低薄膜的生产成本,运用得当,甚至可以达到同时提高产品性能和降低产品成本的双重效果。多层共挤出复合成膜工艺,在生产实践中发挥了越来越大的作用,因此多层共挤出复合成膜工艺也越来越得到软包装界同仁的青睐,成为目前发展多层复合薄膜的首选工艺。当前双向拉伸聚丙烯薄膜的生产中,基本上已经完全完成了由单层双向拉伸向多层共挤出双向拉伸的转变,在聚丙烯流延薄膜的生产中,共挤出成膜工艺也已成为主流工艺;含EVOH层的高阻隔塑料复合薄膜,也毫无例外地采用多层共挤出复合成膜工艺,在量大面广的聚乙烯吹塑薄膜的生产中,也越来越重视多层共挤出复合薄膜生产工艺的应用。
目前多层共挤出复合成膜工艺的产品,已从初始的两层复合薄膜,经三层、五层发展到七层乃至九层结构,虽然随着层数的增加,设备的价格相应提高,但产品性能的提高和成本优势的支撑,使多层共挤出复合成膜工艺,正在不断向多层化的方向发展。成百上千层的超高多层薄膜的生产技术,已开始实用化研究。
多层共挤出复合成膜工艺的产品,除了大量直接应用于包装材料之外,也可用于无溶剂复合、干法复合等贴合型复合工艺的基材,采用多层共挤出薄膜为基材时,可大大减少贴合型复合的工序,简化复合进程,降低产品的生产成本,提高市场竞争力,获取更好的社会效益与经济效益。
二、共挤出复合薄膜生产设备
共挤出薄膜复合设备,除向由多台挤出机替代单台挤出机塑化、并向模头供应多种不同的塑料熔体以及采用特殊结构的共挤出模头替代简易的单层模头之外,共挤出薄膜生产线的组成和配置,包括薄膜的卷取及表面处理(电晕处理、等离子处理或火焰处理等)装置,基本上与单层薄膜生产线相近。共挤出薄膜复合设备基本上与单层薄膜生产线相近,主要差别是模头结构和塑化用挤出机数量不同,多台挤出机以保证不同塑料层原料的塑化、输送和复合成型。共挤出复合薄膜生产设备,有管膜类共挤出复合薄膜生产线(即吹塑共挤出复合薄膜生产线)和平膜类共挤出复合薄膜生产线(亦称流延共挤出复合薄膜生产线)两个大类。
1.管膜类共挤出复合薄膜生产设备
管膜类共挤出复合薄膜生产设备,由多台塑化用挤出机、共挤出管模、吹塑收卷等基本部件组成,为满足后继印刷、复合工艺的需要,通常在吹塑收卷装置中,还有一个电晕处理装置。
管膜类共挤出复合薄膜生产设备,主要有上吹空冷式及下吹水冷式两种。上吹空冷式共挤出复合薄膜生产设备,主要用于聚乙烯类多层共挤出薄膜以及以聚乙烯为主体的多层共挤出薄膜的生产,如LLDPE/mPE+LDPE,LDPE∥PA∥LDPE等;下吹水冷式管膜类共挤出复合薄膜生产设备,主要用于聚丙烯类多层共挤出薄膜,如PP∥PA∥PP薄膜的生产。
多层薄膜共挤出用管模,是管膜类共挤出复合薄膜生产设备的核心部件。按其结构分,主要有套管式和叠加式两大类。
(1)套管式多层薄膜共挤出用管模 套管式多层薄膜共挤出用管模示意图见图2-1。

图2-1 套管式圆管形多层共挤出复合模头示意图
套管式圆管形多层共挤出复合模头开发应用较早,曾被认为是传统的、经典式共挤出吹塑模头,目前应用亦相当普遍,其主要优点是结构紧凑、加工制造方便。
套管式圆管形多层共挤出复合模头,主要的缺点是随着层数增加,模头直径增大,当模头的层数多时,模头会变得直径很大而十分笨重;模头的层数不能根据生产的需要进行变换,例如,不能根据生产的需要,将三层模头变成五层模头;只能从模头的外面,对模头整体(各层)进行加热,不能根据各层树脂的熔点、黏度等特性,对各层进行针对性的温控。除上述缺陷之外,套管式圆管形多层共挤出复合模头,清理也比较困难。因此,多层共挤出吹塑模头,特别是层数比较多的多层圆管形多层共挤出复合模头,有叠加式发展的趋势。
(2)叠加式圆管形多层共挤出复合模头 叠加式圆管形多层共挤出复合模头示意图见图2-2。

图2-2 叠加式圆管形多层共挤出复合模头示意图
叠加式圆管形多层共挤出复合模头,能克服套管式圆管形多层共挤出复合模头的众多缺点,因此近年来有较大的发展,特别是层数多的(五层以上的)复合薄膜多采用此种模头。叠加式圆管形多层共挤出复合模头与传统的套管式圆管形多层共挤出复合模头的比较,见表2-1[1]。
表2-1 叠加式圆管形多层共挤出复合模头与套管式圆管形多层共挤出复合模头的比较

叠加式圆管形多层共挤出复合模头,根据叠加模块的不同,有圆筒状和圆锥状两种,前者的叠加模块为圆筒形,后者的叠加模块为圆锥形。
①圆筒状叠加式圆管形多层共挤出复合模头。图2-3是典型的圆筒状叠加式圆管形多层共挤出复合模头的结构示意图[1]。

图2-3 圆筒状叠加式圆管形多层共挤出复合模头的结构示意图
由图可以看出,每一塑料层与由两圆筒状模板组成的模块相对应。组成模块的两模板中,一块模板的表面上,设有平面形螺纹流道,该平面螺纹流道,将从模块侧面供入的塑料熔融体,供入合流部位,平面螺纹流道的应用,可以最大限度地降低轴向尺寸,从而减小整个叠加式圆管形多层共挤出复合模头的轴向尺寸(模头的高度)。另外,相邻两模块的结合面间,可设置间隙并于每一模块的外侧,设置加热器,使各模块独立加热,据称这样的结构,可以使相邻两塑料层的温度差,在高达50℃的条件下,进行生产。
②圆锥状叠加式圆管形多层共挤出复合模头。圆锥状叠加式圆管形多层共挤出复合模头例见图2-4。

图2-4 W&H公司开发的MULTCONE模头
圆锥状叠加式圆管形多层共挤出复合模头,与圆筒状叠加式圆管形多层共挤出复合模头相似之处,它们均为叠加式结构;不同之处则在于,圆锥状叠加式圆管形多层共挤出复合模头的模块不是圆筒状而是圆锥状,而且模块中的塑料熔体的流道也是圆锥螺纹。
圆锥状叠加式圆管形多层共挤出复合模头有很多优点,可以列举如下:
a.密封性好。圆锥状金属零件的抗变形能力大大高于板状零件,因而圆锥状叠加式圆管形多层共挤出复合模头能有效地抵制熔体高压所引起的变形,因此圆锥状表面的接触、密封效果明显地要优于平面的接触、密封效果。
b.复合产品厚度均匀性好。一方面,如前所述圆锥形零件不易变形,能很好地保持高的加工精度,另一方面,圆锥形零件组合时,具有自动对中的特性,因此圆锥状叠加式圆管形多层共挤出复合模头,可以很好地保持流道尺寸的均匀性,从而有利于保证复合薄膜的厚度均匀性。
c.模头外形尺寸较小。在等长螺纹流道的情况下,圆锥状模块的直径,较圆柱状模块的直径要小得多;生产同样规格的产品,采用圆锥状叠加式圆管形多层共挤出复合模头的直径,可望较圆柱状叠加式圆管形多层共挤出复合模头,减少50%左右。
d.维修方便。圆锥状叠加式圆管形多层共挤出复合模头,无论拆卸、装配还是清理工作,都要比圆柱状叠加式圆管形多层共挤出复合模头方便得多。
圆锥状叠加式圆管形多层共挤出复合模头的一个明显的缺点是,它的轴向尺寸要比圆柱状叠加式圆管形多层共挤出复合模头的轴向尺寸要大。
2.平膜类共挤出薄膜用复合设备
平膜类共挤出薄膜用复合设备,亦称共挤出流延薄膜设备,除以多台挤出机代替一台挤出机塑化供料、以共挤出模头替代单层模头之外,整个生产线的配置,与单层平模的生产线基本一致。流延共挤出模头,从结构上讲,主要有多流道型多层共挤出流延模头与喂料块型多层共挤出流延模头两种。
(1)流道式多层共挤出复合平膜模头 多流道式多层共挤出复合平膜模头见图2-5。

图2-5 多流道式多层共挤出复合平膜模头
该模头中,各熔融树脂层分别在各自的流道(歧管)内流动、展开之后,在紧临近模唇处,汇合成多层层流。
多层层流流动的距离相当地短,不会产生由于多层层流中可能出现的低黏度树脂对高黏度树脂层的包围现象,以及界面不稳定流动所导致的复合薄膜厚度不均匀、透明性下降和纹理等缺陷。多流道式多层共挤出复合平膜模头的优点还有:各层的层厚,可以通过各层的调节螺栓分别进行调节,因而薄膜的厚度比较容易控制;可以用于塑料熔体黏度和温度差较大的塑料间的复合等。
多流道式多层共挤出复合平膜模头的缺点是,体积庞大、结构复杂、价格昂贵、难于用于制造四层以上的多层共挤出复合薄膜。
(2)喂料块式多层共挤出复合平膜模头 喂料块式多层共挤出复合平膜模头,由喂料块(或称连接器)和成型模头两部分组成。各挤出机所供的塑料熔融体,先在被称为喂料块的连接器中汇合,形成多层层流。该多层层流,再进入成型模头中,经成型模头的模口(直线状的狭缝)挤出到成型辅机的流延辊上,经冷却、定型而得到多层复合薄膜,其成型模头部分基本上与普通单层薄膜的模头相同,属单流道型,结构比较简单。保持成型模头部分不变,更换连接器,配之以相应的挤出机,即可得到不同组合的多层共挤出复合薄膜。
连接器型多层共挤出平膜模头见图2-6。

图2-6 连接器型多层共挤出平膜模头
两种多层共挤出复合平膜模头的比较见表2-2。
表2-2 两种多层共挤出复合平膜模头的比较

注:〇良,△可,×差。
连接器型共挤出复合平膜模头,适用范围广,特别适于多层及超多层薄膜的生产,加之维修保养方便以及制造成本较低等方面的明显优势,其使用有日益扩大的趋势。
三、共挤出复合常用原料
原则上所有热塑性塑料,比如聚乙烯与乙烯共聚物(EVA、EEA、离子型聚合物),聚丙烯与丙烯共聚物,聚氯乙烯与氯乙烯共聚物(PVDC),热塑性聚酯(PET、PEN、PETG),热塑性橡胶(热塑性弹性体),等等,均可用于共挤出复合,生产多层塑料复合薄膜。生产实践中,共挤出复合薄膜应用较多的主要是聚烯烃(聚乙烯和聚丙烯)、EVOH、PA、黏合性树脂等。
1.聚烯烃树脂
聚烯烃树脂及其复配物,本身可以通过特定搭配而生产复合薄膜,同时也常常作为热封层和防潮层与EVOH、PA等阻隔性塑料搭配,生产阻隔性复合薄膜。
2.乙烯-乙烯醇(EVOH)、尼龙为代表的阻隔性树脂
乙烯-乙烯醇(EVOH)、尼龙作为氧气、油脂等物质的阻隔性材料,与聚烯烃类塑料搭配,可生产出包装领域所需要的阻隔性良好且具有熱封性的阻隔性复合薄膜。
3.黏合性树脂
聚烯烃类树脂和EVOH、PA等阻隔性塑料之间相容性较差,当它们相互搭配,生产共挤出复合薄膜时,层间的黏合强度较差,甚至没有黏合强度可言。黏合性树脂层的引入,可以使共挤出复合薄膜层间黏合强度大幅度提高,满足使用上的要求。目前所使用的黏合性树脂,主要是乙烯或者丙烯与极性单体的共聚体,如聚乙烯、聚丙烯与马来酸酐或者丙烯酸的接枝共聚体,乙烯与丙烯酸类单体的共聚体以及乙烯、丙烯酸与马来酸酐的三元共聚体等。
四、应用例
1.高阻隔纳米抗菌包装膜的研制与应用
通过挤出复合,可以生产出性能优良的各种功能性复合薄膜,在生产应用中表现出明显的优势,例如利用高阻隔性树脂EVOH和纳米抗菌剂,通过共挤出复合工艺,制备高阻隔抗菌复合薄膜,用于槟榔的包装,较之常规的高阻隔复合薄膜,保质期可延长1倍以上[2]。
(1)主要原料 纳米抗菌聚乙烯。先用分散剂等助剂处理纳米抗菌剂,再与聚乙烯混合,用双螺杆挤出机造粒得到抗菌母料,抗菌母料与聚乙烯树脂共混,得到用于共挤复合纳米抗菌聚乙烯粒料。乙烯-乙烯醇共聚物(EVOH),可乐利公司。黏合层树脂(AD),美国杜邦公司Bynel系列。低密度聚乙烯(LDPE),LD155,上海金山石化股份有限公司。
(2)主要设备 奥地利兰精公司共挤平膜流延机组。
型号:92F057
挤出机:A机,ϕ55,长径比30/1
B机,ϕ40,长径比30/1
C机,ϕ55,长径比30/1
D机,ϕ55,长径比30/1
模头宽度(mm):1350
模口间隙(mm):0.7~1.2
牵引速度(m/min):15~40
流延辊表面温度(℃):15~30
气刀压力(Pa):300~600
表面张力(mN/cm):380~420
产量(kg/h):120~200
(3)工艺条件
加工温度(℃):A机料筒210~250、B机料筒200~240、C机料筒230~260、D机料筒200~240、法兰240~260、机头230~255。
螺杆转速(r/min):A机为80~150,B机为60~140,C机为25~50,D机为70~130。
(4)典型产品
结构:PE(40μm厚)/AD(10μm厚)/EVOH(20μm厚)/AD(10μm厚)/抗菌PE(40μm厚)
性能:抗菌高阻隔包装膜同时具有高阻隔与高抗菌特性,其主要性能指标如表2-3所示。
表2-3 抗菌高阻隔包装膜的主要性能指标

(5)应用 为了较长时间保证槟榔产品的品质,采用抗菌高阻隔包装薄膜与目前广泛使用的铝塑复合包装进行了对比实验:将两种包装材料制作成包装袋,规格为常用的150mm×110mm,每袋64g,然后置于常温下储存,观察外观、香味变化情况。
结果见表2-4、表2-5。
表2-4 纳米抗菌高阻隔槟榔包装与传统铝塑复合包装槟榔的外观随时间的变化

表2-5 包装槟榔香味随时间的变化

从表2-4、表2-5可以看出,传统铝塑复合包装槟榔的保质期在3个月左右,升级为纳米抗菌高阻隔包装后其保质期至少在6个月以上,而且解决了槟榔由于存储时间过长发生霉变的问题。
共挤出纳米抗菌高阻隔薄膜,由原料塑料粒子一次成型为薄膜,成本较为低廉,因此纳米抗菌高阻隔袋与传统铝塑复合袋相比,经济上有较大优势,装64g槟榔的袋子,纳米抗菌高阻隔包装袋的生产成本仅约0.11元,而铝塑复合袋的成本约0.15元。
2.低温热封流延聚丙烯薄膜的研制
潘建等曾通过多层共挤出流延工艺,利用共混料的优势,对CPP流延薄膜的热封合性能进行研究,并取得了较好的实用效果,介绍如下[3]。
众所周知,当采用高速生产线进行自动包装时,对于塑料软包装热封合材料而言,走膜流畅和低温热封性是高速自动包装的两个重要性能指标。所谓低温热封性,指可在封合温度低、封合时间短的条件下可得到合格的封口强度。“低温热封性”要求包装材料的热封层,要有低的始封温度和低的热封温度。始封温度指封合压力1.8kg/cm、封合时间1s,封合强度达到0.5N/15mm所需的温度;热封温度指封合压力1.8kg/cm,封合时间1s,封合强度达到要求的封口强度所需的温度。
封口强度与薄膜材料、厚度有关。在塑料软包装热封合材料中,热封层主要是用PE薄膜和CPP薄膜两类材料,通常PE薄膜的始封、热封温度较CPP薄膜低,但考虑到其他性能的优势(如力学性能、透明度、阻水性),选用CPP薄膜作热封层仍是重要的选项之一。
降低CPP薄膜始封、热封温度,可以通过在热封层混入或选用PE树脂原料,但由于PE、PP的相容性不好,生产的薄膜虽然有较低的始封、热封温度,但会出现分层现象使热封强度难以提高,且在热封层混入或选用PE树脂原料薄膜容易卷曲。因此探讨降低CPP薄膜的始封、热封温度新的技术途径,对优化CPP薄膜的性能与降低CPP薄膜使用者的包装能耗成本均有重要意义。
选用在三层共挤CPP薄膜热封层原料树脂中,共混一定量的弹性体和用茂金属共聚PP作热封层,可以降低薄膜的始封、热封温度。这里介绍加入不同弹性体和茂金属共聚PP的加工性和产品的热封性能的变化情况。
(1)原料 原料一览见表2-6。
表2-6 实验原料一览

(2)样制备 采用三层共挤流延法,制备25μm厚的CPP薄膜样品,其热封层厚度为5μm,制备工艺流程如图2-7所示。

图2-7 CPP流延工艺流程
试验共研究了四个样品:
参考样以三元共聚PP3为热封层;
样品1以三元共聚PP3中混入20%丙烯丁烯共聚弹性体为热封层;
样品2以三元共聚PP3中混入20%乙烯辛烯共聚弹性体为热封层;
样品3使用茂金属共聚PP为热封层。
各样品除热封层原料配方变化外,其他工艺条件都稳定不变,见表2-7。表中AB为开口剂,SL为滑爽剂。
表2-7 CPP薄膜各样品的原料组成

(3)性能评价方法 热封强度的测试按QB/T2358—1998《塑料薄膜包装袋热合强度试验方法》,在美国SENCORP SYSTEMSINC制造的12AS/1型热封试验仪进行;封合压力18kgf/cm,封合时间1s,使用广州试验仪器厂制造的XLW-100型微控电子拉力试验机进行封合强度的测试。
(4)结果与讨论
①不同配方的加工性能为进行加工性的对比分析,各样品的生产按:参考样-样品1;参考样-样品2;参考样-样品3的顺序生产。
在生产样品1时发现,当热封层加入20%丙丁共聚弹性体后,熔体压力有4%的下降,后又回升到原压力值;薄膜纵向出现间断紊流,紊流宽度约占横向膜宽的2%,1~2min后紊流消失。丙丁共聚弹性体加入后除了换料的波动外,其他无明显变化,该配方加工性好,原因可能是丙丁共聚弹性体与PP有很好的相容性,且选用的熔融指数与相混的PP3相同。
在生产样品2时,当热封层加入20%乙辛共聚弹性体后,薄膜雾度明显增大,纵向出现连续紊流,紊流宽度约占横向膜宽的9%,在样品试制的整个过程中(约40min)紊流都没有减少,热封层挤出量下降13.4%;切边料破碎后回收困难,回收挤出机电机负载从33%升到55%,收卷粘连,该配方加工性不好,原因可能是乙辛共聚弹性体虽然其与PP的相容性与PE比较有很明显的改善,但仍不能达到很好的相容,使薄膜雾度增大;选用的熔融指数较共混的PP3小,使得热封层挤出量下降;乙辛共聚弹性体自黏性大,切边料中有一定含量后,使得回收加入困难;薄膜柔软,收卷粘连。
在生产样品3时,热封层料更换茂金属共聚PP后,熔体压力上升了3.5%,其他无明显变化,原因可能是茂金属共聚PP分子量分布窄,熔体黏度大。
综上所述,样品1和样品3与参考样加工性相当,样品2加工性较差。
②热封性能。各样品测试的始封、热封温度及相应的封合强度见表2-8、表2-9。
表2-8 各样品始封温度及相应封合强度

表2-9 各样品热封温度及相应封合强度

注:25μm厚CPP薄膜热封口强度要求≥8N/15mm。
从表2-8可见,样品2的始封温度最低,较参考样降低12℃;样品1、样品3始封温度也较参考样分别降低了4℃和7℃。从表2-9可知,样品3的热封温度最低,较参考样降低12℃;样品1、样品2热封温度也较参考样降低了6℃。由于各样品除热封层树脂配方有变化外,其他工艺稳定不变,样品1、样品2都在热封层加入了低熔点的弹性体,样品3使用的茂金属共聚PP熔点较三元共聚PP3低,因此低熔点的弹性体加入,可以降低成膜产品的始封温度与热封温度:同样的加入量,熔点愈低的弹性体使成膜产品的始封温度降得愈低,但热封温度不因弹性体熔点低而随之降低,这与弹性体的力学强度有关:相对熔点较低的茂金属共聚PP树脂成膜后,产品的始封、热封温度也相对较低。
(5)应用 热封层加20%低熔点的弹性体,可以明显降低CPP薄膜的始封温度与热封温度。相对熔点较低的茂金属共聚PP作热封层原料,较一般三元共聚PP生产的CPP薄膜的始封温度、热封温度低,且二者加工性相当。在低熔点弹性体的选择上,还需考虑与PP的相容性,如果相容性不好,产品始封温度、热封温度虽然会有降低,但同时也会降低产品的一些其他性能,特别是产品的外观。
低温热封流延聚丙烯薄膜可以与PET、BOPP、VMPET等薄膜进行多层复合使用,也可直接印刷、作为热封包装使用。该低温热封流延聚丙烯薄膜可应用于休闲食品、药品等商品的包装。由于该热薄膜的低温热封性,包装时可节约热封的电能、延长热封模具及与加热相关部件的使用寿命,还可大大提高包装速度,从而提高生产效率。在使用旋转切刀的高速包装线上,对包装材料要求低温热封的同时,还要求包装薄膜有一定的刚性,低温热封流延聚丙烯薄膜比柔软的PE有更好的包装适用性,因此更具竞争力。
3.五层共挤出输液袋用薄膜
输液或血液等类医疗用品至今仍大量使用软聚氯乙烯薄膜。软聚氯乙烯薄膜由聚氯乙烯树脂中添加各种助剂制得,聚氯乙烯树脂中单体的含量及各种添加剂卫生性能的控制,一直是备受关注和人们非议的问题,使用性能更佳、卫生安全性更为可靠的多层共挤出输液袋用薄膜用复合薄膜。近年来颇引人注目。国外发达国家,共挤出输液袋用薄膜已成为一个工业化产品,在实际应用中大量使用,取得了良好的实效;国内共挤出输液袋用薄膜的工作起步较晚,目前应用也还比较少。陈亦锋在中国专利中,披露了一种五层共挤出输液袋用薄膜的制造方法[4]。
根据专利披露的情况,这里向读者作一个概略的介绍。
该发明的多层共挤输液膜,为五层结构。其特征在于:
第一层为封内层A,其成分是聚丙烯与SEBS热塑性弹性共聚物组成的混合树脂,SEBS为苯乙烯-乙烯-丁烯橡胶-苯乙烯嵌段共聚物,且SEBS热塑性弹性共聚物在混合树脂中的加入量为40%~60%(质量分数);热封内层A中所用聚丙烯与SEBS热塑性弹性共聚物组成的混合树脂的熔融指数为2.0~15g/10min,密度为0.89~0.9g/cm3;该层厚度为20~45μm,占多层共挤输液膜总厚度的15%~25%。SEBS弹性体为苯乙烯-乙烯-丁烯橡胶-苯乙烯嵌段共聚物,由于丁烯橡胶的弹韧性特别好,所以不但成品柔软性和强韧度极佳,低温热封性能也很好。SEBS用在内层还具有自粘作用,在膜泡内用100级无菌超净空气吹制,经夹棍压扁后,能使两层膜始终在自粘闭合的状态下分切包装,杜绝外界低净化级别的空气污染,从而保证了直接接触药液的内层具有优良的卫生和生物指标。经药物相容性试验证明,它耐化学稳定性能特别好,具有广泛的药物相容性,灌装药液后经微粒仪在6个月的加速试验中检测证明,渗出物和微粒数极少,完全达到和超过了欧美及国家标准。
第二层为粘接层B,其成分是丙烯-乙烯共聚物,熔融指数为1.5~5g/10min,密度为0.89~0.9g/cm3;该层厚度为15~26μm,占多层共挤输液膜总厚度的8%~15%。该层作用是对第一层A和第三层C原料具有良好的黏结强度,使它们不管是低温储藏,还是高温灭菌始终结合在一起。
第三层为核心层C,其成分是丙烯-乙烯/α-烯烃共聚弹性体,熔融指数为1~5g/10min,密度为0.89~0.92g/cm3;该层厚度为50~80μm,占多层共挤输液膜总厚度的30%~45%。该层特点是柔软度特别好,能耐冲击和弯曲,透明度和耐穿刺极佳,在低温下仍能保持良好的韧性,垂伸强度和力学性能好,是能保证通过2.5m跌落实验的主要材料。
第四层为粘接层D,其成分是乙烯甲基丙烯酸酯聚合物,熔融指数为1.5~ 5g/10min,密度为0.9~0.93g/cm3该层厚度为15~25μm,占多层共挤输液膜总厚度的8%~14%。该层质地柔软,冷热稳定性好,对第三层C和第五层E原料具有良好的粘接牢度。
第五层为耐候层E,其成分为弹性树脂聚对苯二甲酸乙二醇酯,熔融指数为4~10g/10min,密度为1.1~1.3g/cm3;该层厚度为18~36μm,占多层共挤输液膜总厚度的10%~20%。聚酯具有良好的阻隔性能和耐冲击强度,透明度好,强韧耐磨,冷热稳定性能好,在高温热封和高温杀菌时不会变形,并以优良的物理性能,保证外层的耐摩擦性能和印刷牢度。
众所周知,聚酯的熔点温度为225~260℃,丙烯的熔点温度为164~172℃,乙烯的熔点温度是125~128℃,用聚酯作为外层,能利用它的耐高温性能,解决了很多专利中所谓的对称结构(即内外层都用丙烯或乙烯)在实际应用的热封制袋时会碰到的困难,如外层树脂熔融温度与内层差不多的话,热合时温度低了根本烫不牢,如把温度调高到内层树脂能熔融粘牢的时候,外层树脂先接触烫模,因经不起长时间的高温而变形,甚至破裂,尽管温度、时间、压力微调得很仔细,由于输液膜的厚度大,总是感觉外面的膜快熔破了,而传递到内层的热合温度还不够,这样热合成袋的平整度肯定不好,漏包等次品比例也很高。
陈亦锋等在大量的生产实践中分析研究,结论是内层A树脂在能经得起高温121℃、30min灭菌的同时,应选用熔点温度应尽量低的树脂,加入SEBS,满足了这方面的要求,同时外层必须选用能耐高温的聚酯,才能保证制袋质量和输液袋上烫印文字的效果,随着外层温度适应范围的宽广,就有把握提高制袋速度,在保证内层热封效果的同时,也提高了生产效率。
聚酯不但透明度和透光率好,还有着良好的阻隔性能和拉伸强度,聚酯的氧气透过量比聚丙烯少25倍以上,比聚乙烯要少50倍以上,这就是用了聚酯后,拉伸强度和透氧、透湿等物理性能大幅提高,输液膜的厚度降低了,还有把握达到国家标准的理由之一。
所述多层共挤输液膜的总厚度为150~190μm。
与现有技术相比,该法的优点在于:
①内层具有自粘性能,在收卷、分切包装出厂时始终密闭,卫生性能好,微粒数极低,渗出物极少。
②透明度和柔软性极佳,可完全压扁,避免瓶装输液空气交换带来的药物污染。
③耐121℃高温灭菌30min,不漏液,物理性能不下降,在低温环境下仍能保持良好的韧性,解决了玻璃瓶不能冷藏的难题,尤其是经高能电子辐照处理后的多层膜,其在此方面的表现尤佳。
④和氧气透过率低,阻隔性能好,可以做成双室袋或多室袋,在同一袋内灌装不同药液,用力一拍即可混合,减少配药时间,方便医院使用。
⑤广泛的药物相容性,不会与药液起不良反应。
⑥热合强度高,渗漏率低,适应各种自动灌装机高速连续生产。
⑦耐穿刺和冲击性能好,抗2.5m跌落实验。
⑧环保材料,生产、使用及回收中不产生毒素。
五、共挤出复合的局限
前面讲了许多共挤出复合工艺的许多优点,并指出共挤出复合工艺是生产多层复合薄膜的首选工艺,但和所有事物一样,共挤出复合工艺并非完美无缺,可以由它“包打天下”,由它解决复合软包装材料生产的所有问题,共挤出复合工艺也有其重大的缺陷,只有用其所长,和其他复合工艺特别是和无溶剂复合、干法复合等贴合型复合工艺相配合,取长补短互为依托,才能充分发挥现代复合工艺的优势,促进塑料软包装行业的发展。
共挤出复合工艺有一个重大的无法回避的缺陷,那就是共挤出复合工艺是只能用于生产由各种热塑性塑料组成的复合薄膜,对于含有纸张、铝箔或者含有金属、无机蒸镀层等等非热塑性塑料层的复合薄膜,则绝对不可能采用共挤出工艺生产的;另外当复合薄膜需要里印时,也不可能仅仅依靠共挤出复合工艺制得,因为共挤出工艺从塑料原料的粒子(或粉体),直接制得多层复合薄膜,层间印刷自然是不可能的事。生产含有纸张、铝箔或者含有金属、无机蒸镀层等等非热塑性塑料层的复合薄膜以及需要里印的复合薄膜,要生产这些材料,都是共挤出复合工艺本身固有的、不可逾越的红线,而生产这类材料,正是无溶剂复合、干法复合等复合方法英雄用武之地,因此当我们开发新品,选用复合工艺的时候,在首选共挤出工艺的原则下,还应当高度重视无溶剂复合等复合工艺,通过共挤出工艺、无溶剂复合工艺或者它们的合理匹配,以获取最佳的社会效益与经济效益。